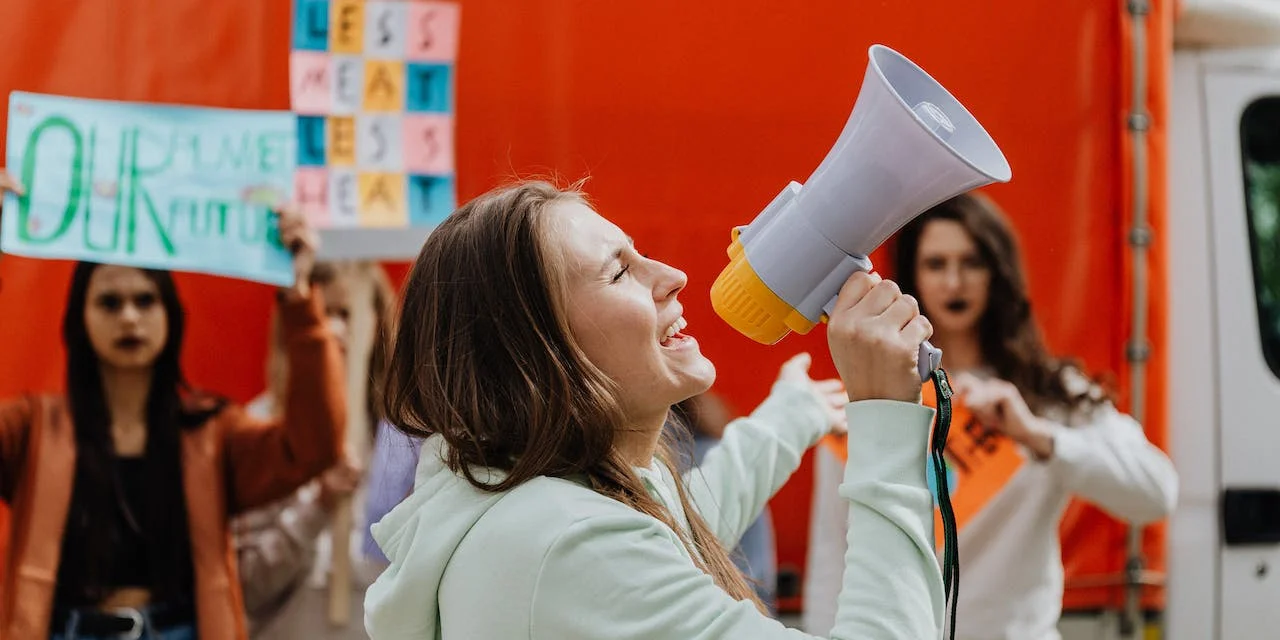
SLB (NYSE: SLB) today announced an investment and technology partnership agreement with Geminus AI that will give SLB exclusive access to deploy the first physics-informed artificial intelligence (AI) model builder for oil and gas operations. The Geminus model builder fuses physics-based approaches with process data to produce highly accurate AI models that can be deployed at scale, far faster and at much less cost than traditional AI approaches.
“The investment made by SLB in its partnership with Geminus AI produces a step-change in operational performance for customers, from production pipelines to facilities,“ said Rakesh Jaggi, president, Digital and Integration, SLB. “Geminus’ capability to fuse AI methods with physics-based simulation data will empower customers to quickly and easily create hybrid models of their operating assets that can be optimized in real time against numerous outcomes, such as opex reduction, increased productivity, and carbon emissions minimization.”
The Geminus platform uses novel, physics-informed AI computing to translate constraints of the physical world inside digital models. It requires only sparse data, and models are easily updated with the infusion of new data points. Data scientists and modeling engineers can use the platform to predict the behavior of complex systems and make informed real-time decisions.
“We see our partnership with SLB as invaluable to helping us unlock value for the energy sector,” said Greg Fallon, CEO, Geminus AI. “With thousands of oil and gas processing facilities and complex well networks held by hundreds of different customers, SLB’s relationships and reach will help us deliver significant efficiency and productivity increases for customers.”
In a customer use case, SLB delivered a Geminus hybrid AI-driven application to optimize economic performance while reducing carbon emissions at a natural gas plant. The application, created by Geminus’ physics-informed AI solution, was trained by data from SLB’s Symmetry™ process simulation software. It took just days to create, including the underlying hybrid AI model, and has the capability to evaluate 20,000 complex scenarios in under a tenth of a second. The application enables operators to interactively explore the impact of changing process settings on the plant’s carbon footprint and yield. In other use cases, the technology has vastly improved the efficiency of fluid catalytic crackers—the heart of an oil refinery—and improved the performance of electric submersible pumps and industrial wellsite chokes.